Revolutionizing the Pointe Shoe
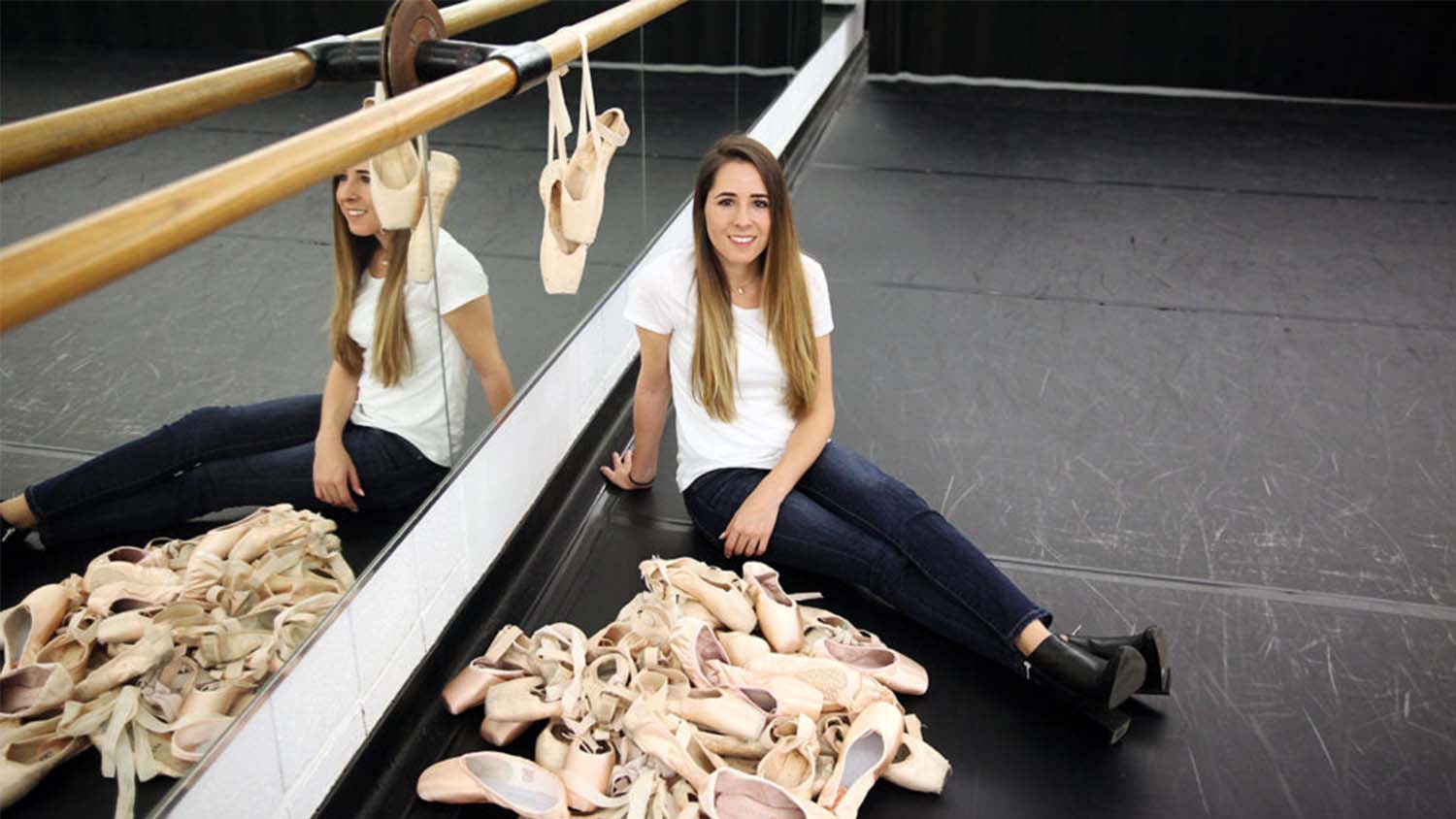
By Julie Watterson
Brittany Buckner’s research aims to revolutionize ballerinas’ pointe shoes, making them less expensive and more durable. Inspired by three young ballerinas in her family, she has dedicated her Master’s of Science in Textiles research to evaluating the challenges of pointe shoes. Thanks to funding from the Osborne Foundation, she plans to continue her studies at NC State University’s Wilson College of Textiles and focus her Ph.D. work on redesigning the pointe shoe.
Buckner discussed her journey and what led her to Textiles as well as the focus of her research: common problems encountered by consumers of pointe shoes. She hopes to collect data by surveying ballerinas and dancers. The survey is open through July 29. Respondents under the age of 18 are welcome to respond but will need their parents’ permission.
As an undergraduate, she studied Apparel Design and Merchandising at Appalachian State University after starting out as a theater major at Lenoir-Rhyne University.
When pursuing a graduate degree what brought you to the Wilson College of Textiles?
NC State’s reputation for having the best textile school not only in North Carolina, but within the United States.
What inspired you to focus your research on pointe shoes?
My three little sisters are ballet dancers, ages 9, 11 and 13. My mother gave me a pair of pointe shoes and said, “I am tired of paying $80 per pair every three months for two children and soon I will be buying for three.” She said, “Take these to school and figure out how to make them cheaper or last longer or both.” I accepted my mother’s challenge and decided this would be my topic. Now, as the 11 and 13 year olds have advanced in pointe since this began, she is paying $120 per pair every three months and they have to have multiple pairs when it is showtime. Two to three pairs each for eight to 10 performances, two times a year.”
What are common issues with pointe shoes?
There are many! I think someone could do a thesis on each issue. Below is a small overview of the main issues I am focusing on.
Comfort: You have to purchase additional “accessories” such as toe pads, toe spacers, gel squares, lambs wool, and the list goes on just to make them wearable. Even with all these additions, many still get blisters and experience other types of pain.
Cost: Average ballet student/parent pays $80-$120 per pair. Pro companies get a lower wholesale price of around $67.
Construction: They are currently handmade so when ballerinas order three to 50 pair at a time, there are usually inconsistency issues.
Durability: They last a maximum of 20 hours. Professionals wear one pair per day, on average, and sometimes more that one pair for a show if there is a lot of pointe work involved. An average student can wear them for up to three months.
Materials: The shoes are currently made of some combination of cardboard, cotton, wood glue, plaster, and paper. These materials are all outdated, non-durable, non-breathable materials that break down with moisture/sweat. The outer fabrics are a slippery satin and suede or leather outsole.
Medical: Most ballerinas have distorted feet because of the shoes. Many also get bunions, ingrown toenails, toenails falling off, etc.
Preparation: They do not come ready to wear. For every new pair, the ballerina herself must sew on the ribbons and elastic in addition to breaking them in. Every dancer has her own rituals whether it is banging them in a door, cutting parts of the shoe off, adding super glue for stability, darning the platform, etc.
Sustainability: As you can see, ballerinas go through tons of pairs. NYC Ballet goes through over 7,000 pairs per year for 47 female dancers. That is just one professional company out of hundreds in the United States and not counting all the aspiring students.
Symmetry: If everything isn’t bad enough, there is no difference between left and right, so you must label each new pair so you don’t get them mixed up.
As you focus your Ph.D. work on redesigning pointe shoes, will you reach out to local ballerinas?
Of course. Reaching out to local ballerinas to take the survey and get their personal opinion(s) on the issues will be my primary work this summer. I hope to use them for testing purposes when a shoe comes to fruition.
Are any made in the U.S. or are they sourced and manufactured in many other countries?
Both. Capezios were handmade in the U.S. up until a few years ago. When they had such an issue with inconsistency, they moved operations to Thailand, where they are still handmade. Gaynor Mindens are made here in the U.S. still. Grishko and Russian Pointe are made in Russia. For the most part, the vital information is that they are handmade. The materials are manufactured, but hand assembled. Most professional companies have a contract with a brand, similar to Nike and individual basketball players, except with ballet companies. For example, NYC ballet uses Freed of London, which are made in England. Each ballerina chooses a “maker” or cobbler. Each cobbler in the Freed factory has a symbol which represents them, such as a clover, butterfly, spade, diamond, fish, etc. When the NYC ballet orders for each ballerina, the order form will have her specific requests given to her chosen “maker.” These symbols can also be seen on the bottom of each shoe along with the month they were constructed in.
How do you hope to reduce the cost and provide more durability? Will this ultimately include a change of materials and manufacturing processes?
Yes. I hope to reduce the cost by using technologically more advanced materials, which will in turn also provide more durability. Even if the cost is only reduced by a small amount, say $80 to $65, the number of shoes being purchased will be reduced, saving money in the long run. To deal with the inconsistency issue and cost, I would prefer to have the manufacturing process reduced to as little human manual labor as possible. The human manual labor will ideally be transferred to human design labor and machine operations.
What would you say to others who may be interested in pursuing graduate programs at the Wilson College of Textiles?
If you have any type of desire to see a change in anything textiles related or want to know how the industry works, I would say go for it, and you will go from being a jack of all trades to an expert on the textile subject that you find most interesting.
- Categories: