The Treasure Beneath the Wilson College of Textiles: The Model Manufacturing Facility
August 17, 2022
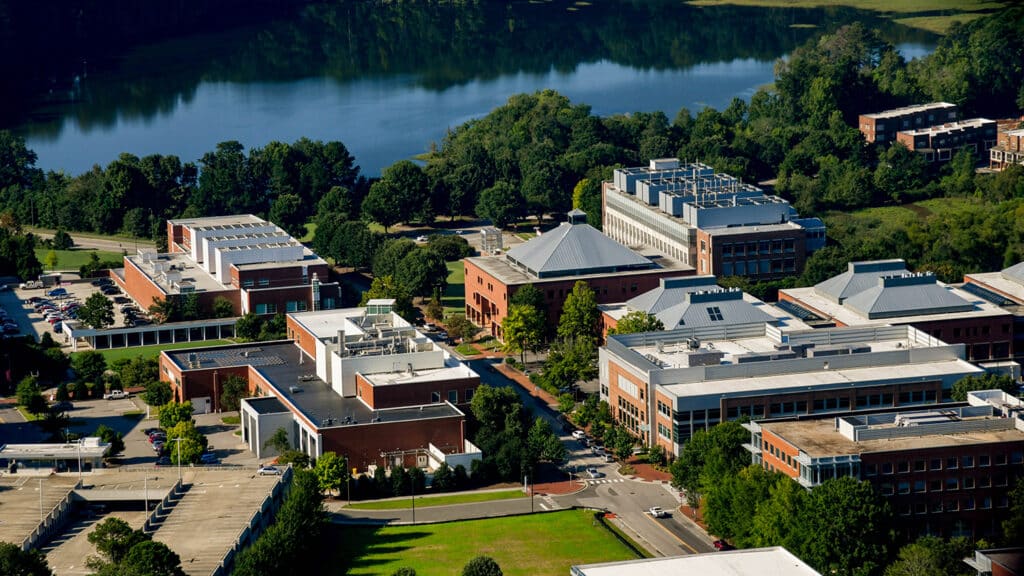
By Rachel Raineri
If you have been a student at the Wilson College of Textiles or have had the opportunity to take a tour of the labs, you may have gotten lost in the basement within those halls that seem labyrinthian. What may not have been obvious at the time is that you were walking through a gold mine for the textile industry; Zeis Textiles Extension’s labs, or the Model Manufacturing Facility, not only support the college’s academic mission but provide fabrication and testing services to textile companies.
In simple terms, its value is the result of a combination of a few factors. In large part, it is because, not only is the entire textile production value chain housed in those labs, but they have pilot-scale capabilities with access to a variety of traditional and innovative machinery.
Furthermore, the true worth of this is realized because of the expertise represented in the personnel, with tangible evidence within the number of varied projects they are completing at any given time, projects for both industry and academic purposes.
We’ve already understood the magnitude of its value based on its contributions to both the economic growth and environmentally sustainable development of today’s textile sector, however, the true reach of the Model Manufacturing Facility is more expansive in that it plays a continued role in developing the textile sector of tomorrow and its leaders. Although many effects of the grand overseas shift of the textile sector from the States in the 1970s are lasting and yet to be explored, we must also recognize that efforts to bring textiles back to the United States and with greater innovation are growing and that the gold in the basement of the Wilson College of Textiles is pivotal to that growth.
Entire Value Chain with Pilot Scale
The key to making an idea a reality is iteration— trial and error at a small scope, fine-tuning, and adjusting. While this process may look different at the scale of an undergraduate final project and an emerging company, it still requires machinery and time to produce it. Representing a complete value chain, ZTE labs include Yarn Spinning to Knitting or Weaving, then Dyeing and Finishing, with Physical Testing to evaluate.
For a company or idea that requires passing through multiple steps in the value chain and the validation of testing, like Natural Fiber Welding, having all labs housed under one roof, “makes it much easier to go from trial to testing and cut down on time and cost for transportation,” commented Gautam Alashe, Clarus Product Engineer at Natural Fiber Welding. Natural Fiber Welding is aiming to change the way material is made, making high-performance plant-based materials. Having worked with small samples in the Spinning, Knitting and Weaving labs, it was imperative for them to then see how their materials respond to dyeing and finishing.
“NC State is unlike other universities in that it has dyeing and finishing capabilities, at both large and small scale,” says Gautam on why Natural Fiber Welding chooses to work with NC State, “and it also has the ability to test for the whole yarn to fabric hierarchy.”
For others like Sally Fox, a self-proclaimed Don Quijote, and naturally colored cotton breeder, using the labs at NC State is an incredible option as her quantities are often too small to be done on an industrial scale. Sally’s research on organic and sustainable colored cotton as a means of reducing pesticides in the field and dye-waste in processing is funded by selling products made from it. “I have a profound appreciation for NC State because it is a place that gets things done! And I wouldn’t be able to get my yarn carded, plied, or spun otherwise,” Fox says with an enthusiasm that’s always marked in her voice.
Machine Capabilities and Relationships
While Sally was grateful for the custom ring-spinning, and Natural Fiber Welding was excited about the back winder machine, there are a plethora of different relationships developing around the machinery in the labs. Many machine companies, like Baldwin finishing and Sheima Seiki knitting find the relationship of keeping their equipment within the labs to be mutually beneficial, as it gives exposure to their technology for research and industry projects.
“There is a lot of effort right now to bring knitting back to the US, to create highly technical fabrics on highly technical machines,” says Jenna DeCandio, manager of the knitting lab. From the sock robot to i-plating in knitting, to the jacquard weaving of stop motion film squares, there is endless possibility threaded into all of the machinery in each of the labs. Wilson College’s Kate Nartker’s unique jacquard weaving project, for example, involves exploring the narrative nature of textiles in a 3-5 minute woven animated short.
While traditional machinery is being used for innovation, there is also an emergence of innovative machinery that can drastically change textile processing. The BaldwinTexCoat G4 applies traditional finishes with spray valve technology, reducing water, drying time and energy used by up to 50%, and recycling all chemistry used. Another instance is Apjet Inc., who uses its patented plasma technology to dye and finish with no pollution or waste water and less energy, heat and chemical use. ApJet has some machinery housed in the Dyeing and Finishing lab and has such unique capabilities as being able to inkjet print finishes.
Carrie Cornelius, V.P. of Technology at APJeT, Inc, when asked about the benefits of a machinery partnership with Wilson College gave a resoundingly similar statement to all other aforementioned companies saying it is “a great resource in terms of knowledge, skills, chemistry, resources, facilities, and of course the expertise of all the faculty.”
Expertise and Education
What good would machinery and possibility be without the know-how to fruitfully utilize them? “Having knowledge and expertise gives you value that makes you indispensable,” says Tim Pleasants, Sr. Lab Operations Manager and Spun Yarn Lab Manager, while he also highlights that the biggest component of the labs is education. Each lab has no shortage of industry projects, running multiple projects at a given time where they are able to educate and help companies prototype and test. Additionally, the student workers who work on those projects are gaining training and experience running machines.
Beyond student workers, the labs also give tours, teach classes, and provide resources to undergraduate and graduate students to conduct research and develop capstone projects. This allows students the opportunity to put the knowledge they have gained in their classroom studies to practical use and familiarize themselves with machinery.
Not only does this develop valuable leaders with sharpened skills, but as they graduate and enter the workforce, that machine knowledge goes with them. The ideal crossover found in the labs is between machines and projects that are changing the industry and the industry leaders of the future who know them and how to utilize them.
Through a combination of focus on education and drive for research and innovation, Zeis Textile Extension serves to bridge the gaps between generations and between industry and academia. During a time of rapid development, these labs open the door for both current and emerging textile companies as well as students to take advantage of the knowledge, expertise, and possibility within them to fuel the current landscape and cultivate the future of textiles.
To this end, the needle is continuously being moved forward by ZTE as they expand in the near future with the addition of the Flex Factory, a space that stands in the center of the academia-industry Venn diagram. It will have machinery for on-site rapid prototyping including 3-D printers, body scanners, and spinning. Additionally, it will have classrooms, showrooms, and collaborative spaces for both students and manufacturers.
“We want to develop this Flex Factory as a seed of ideation, innovation, collaboration and sustainability allowing a one-stop-shop without the hindrance of resources such as high-tech equipment, knowledge, expertise, and supplies, for all, industry, researchers, start-ups and students alike,” says Andre West, director of Zeis Textiles Extension. Wilson College has likely touched your life in one way or another already and is always welcoming visits and more active connections, so you may have the opportunity to take part in the treasure.