Non-stop Innovation: Researchers Patent Weaving Efficiency Process
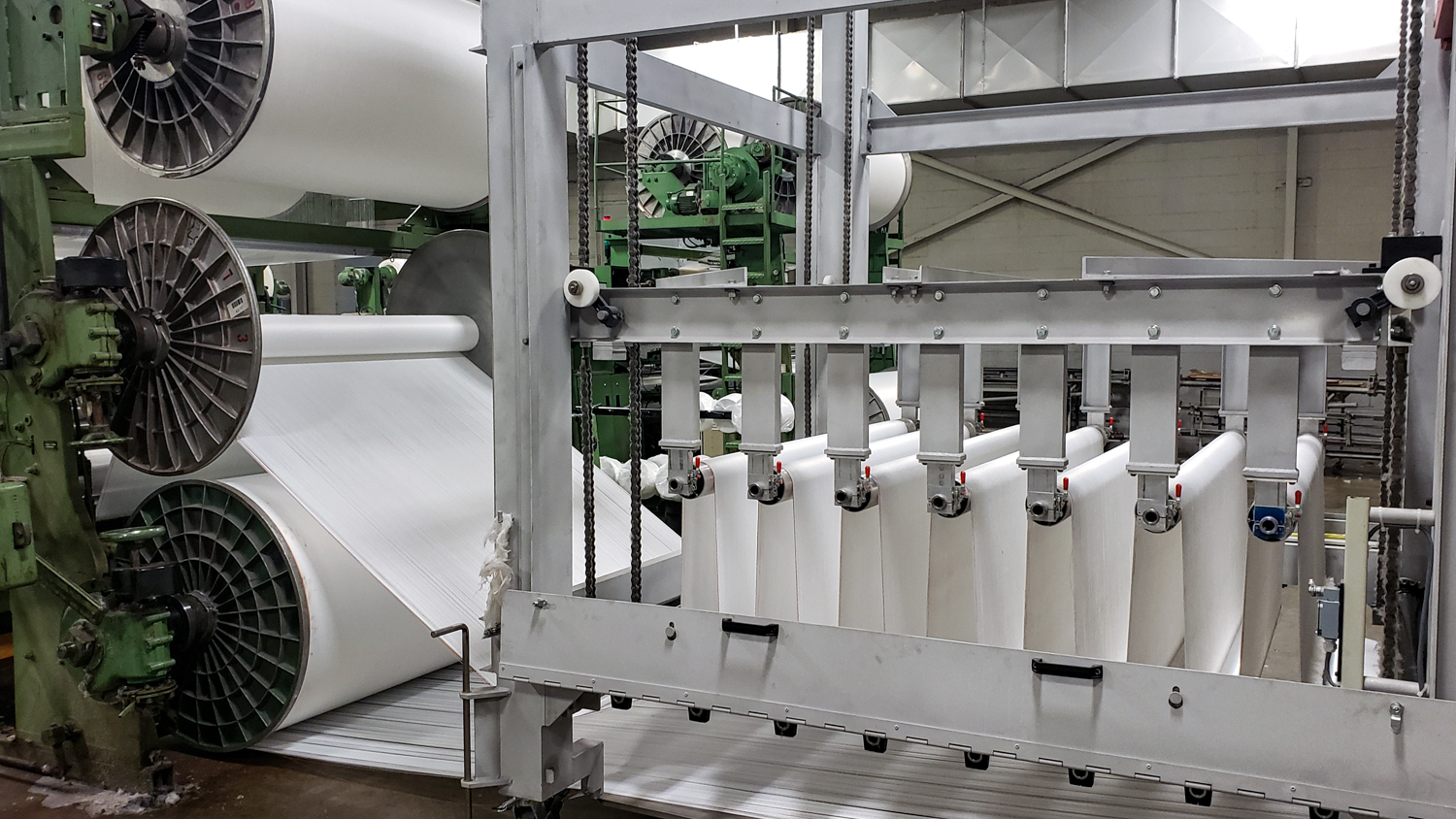
Patience and persistence power innovation.
Since the first industrial revolution, the weaving industry has made significant advances to increase the productivity and efficiency of its machines as well as the quality of the fabric they produce. This has been accomplished through improving the quality of the yarns and increasing digital automation, control and monitoring. Today’s weaving machines are ready for the fourth industrial revolution. However, these advances in weaving have mainly targeted elimination and reducing short-term weaving stops.
Two long-term downtimes have remained unchallenged: the tying-in process and the drawing-in process. Previously, improvement in tying-in machines targeted knotting automation and knotting speed and diversification of handling different yarn types. While the weavers appreciate the advances in tying-in technology, the weaving process has to be stopped for a long time during the tying-in of ends from the depleted warp beam to the ends from a full warp beam.
For decades, Charles A. Cannon Professor of Textiles Abdel-Fattah Seyam and William Oxenham, the Abel C. Lineberger Distinguished Professor Emeritus in the Wilson College of Textiles, have known about this time-draining problem for weavers. These professors have many years of experience in all aspects of yarns and fabrics, including yarn-machine interactions, and have designed and constructed apparatus and equipment for assessing yarn tension.
High-speed weaving machines require frequent tying-in. Stopping high-speed weaving machines frequently for such a long time is a premium. The lack of efficiency impacts the cost and hence the industry’s competitive edge, too. An initial study on time loss during tying-in revealed that the weaving process stopped for three to six hours for approximately 3,000 to 6,000 warp ends, respectively.
Although the problem isn’t a new one for the weaving industry, industry and researchers remained perplexed as time passed. Did they need to stop the weaving machines for so long each time?
No.
Wilson College of Textiles Professors Seyam and Oxenham had a solution. They also had support for a now-patented idea for their non-stop tying-in process. Then came the next step:
“Solutions need resources,” says Seyam, who is also head of the Department of Textile and Apparel, Technology and Management.
With a solution on paper, Seyam and Oxenham sought support. When they learned about the call for proposals from the Walmart Manufacturing U.S. Innovation Fund and saw that improving weaving efficiency was one of the research areas included, they submitted what would become a winning proposal to improve weaving efficiency via the development of a “non-stop tying-in process.” The funding organization awards proposals that can enhance U.S. competitiveness and create more jobs.
Today, the duo holds a patent for their process (US 10,982,357 B2). The innovation could increase weaving efficiency by 4-6%. Such an increase in efficiency could not be achieved by all other innovations targeting short-term stops combined.
Collaboration in the Carolinas
Using sample warping and weaving machines, the professors first tested their prototype equipment of a splittable accumulator and “tail beam” support, along with developed procedures, at the Wilson College of Textiles Weaving Lab. The concept worked, but they needed two more things: a full-scale prototype and a place to perform full-scale trials.
P&A Industrial Fabrications in Roxboro, North Carolina, offered its plant to host trials. The company manufactures premium velvet woven fabrics for paint rollers. These products require three warp beams; the need for the tying-in in such cases is more demanding compared to fabrics that require one warp beam.
It was a new opportunity for Todd Fleming, a process engineer for P&A Industrial Fabrications.
“It was exciting to know we might come up with a solution that many weave rooms could use,” Fleming says.
Next, Seyam and Oxenham found a manufacturer that was willing to collaborate and build a full-size accumulator to their specifications. They only needed to look a bit further south. The search stopped with Menzel USA, a Germany-based company with its only U.S. location in Spartanburg, South Carolina.
“We do custom equipment,” Don West, a sales engineer for Menzel USA, says. “We look at a customer and we determine their needs. We propose and design based on what the needs are.”
The Carolinas connection was a perfect fit. Seyam and Oxenham had a manufacturer and a place to test their now-patented process. While the concept worked, one challenge remained: maintaining tension after the tying-in is complete and the accumulator starts to feed the warp to the weaving machine. Another major life event would put a pause on the project: the COVID pandemic. Every part of the world was impacted, including the weaving industry. With the non-stop tying-in process proven to work, things began to feel stop-and-go. Supply levels changed, and plant personnel changed, too. The determination of the collaborators led to conducting a successful recent trial at P&A Industrial Fabrications but not without the expected issue with the prototype, primarily associated with warp tension control by the accumulator.
The accumulator stores and releases the warp sheet during the tying-in process, while the weaving process continues without stopping. One important detail is how the tension level must remain the same when the accumulator starts to feed the weaving machine.
“Because it is a portable process, the accumulator is removed,” West describes. “The challenge is how you can maintain tension while taking the accumulator away from the process.”
Moving forward
The recent trial revealed a few modifications of the current prototype that would lead to a final accumulator design with warp sheet tension as top priority. The range of warp tension provided by the accumulator needs to be critically controlled. The team is working together to move forward with modifications to the prototype accumulator and then schedule another trial.
Involving students
Seyam and Oxenham value the education mission and mentoring of students. Several students and postdoctoral researchers were involved. They were provided the opportunity of learning about the emerging non-stop tying-in process that addresses an industry-wide problem requiring a solution.
Students don’t just hear about problems. They collaborate with professors, too. Experiencing the ups and downs of innovation provides a real-world view of what is necessary to bring about improvements in an established process.
- Categories: