Diagnosing Amputee Discomfort
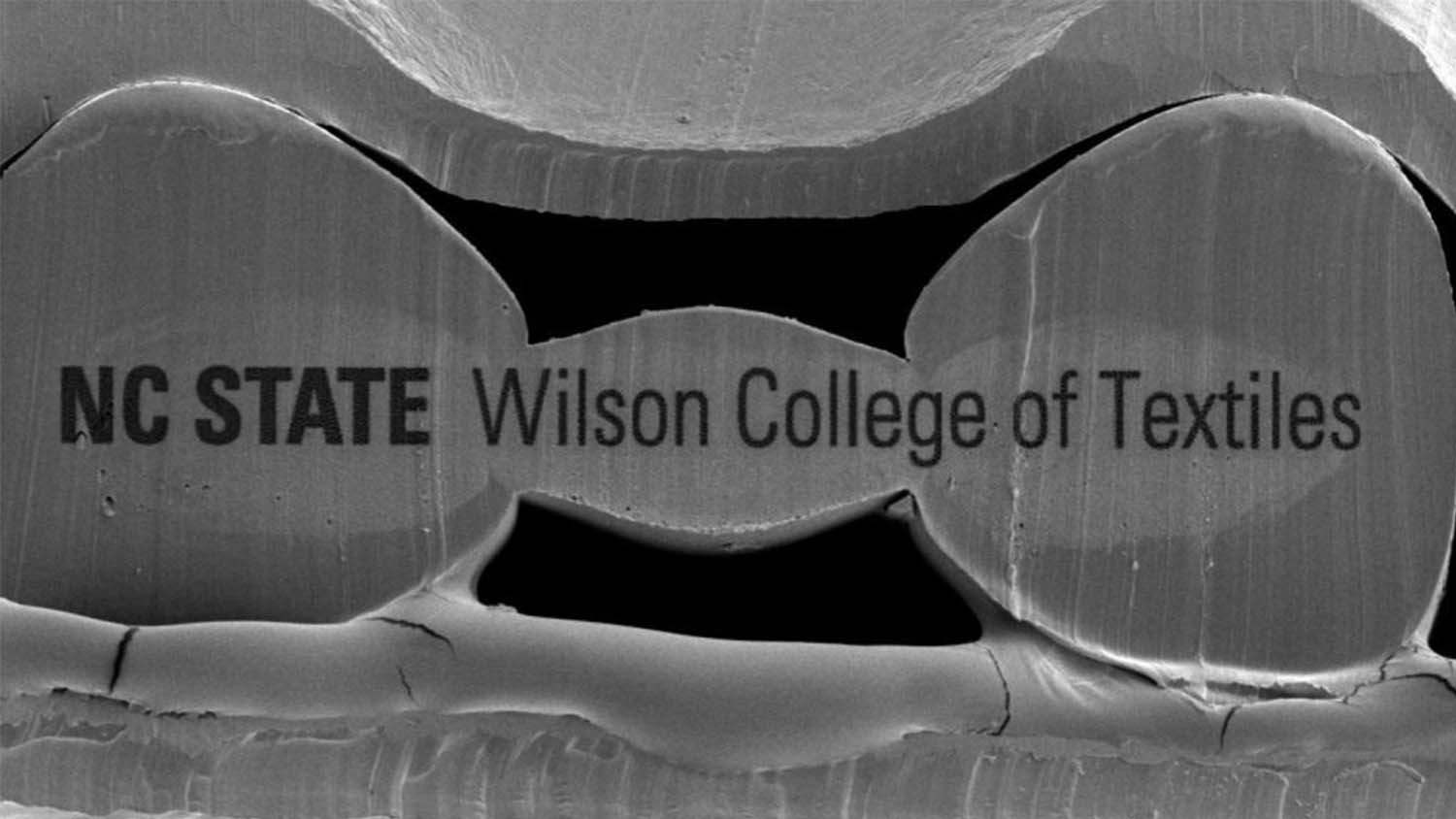
Written by: Cameron Walker
Researchers at the Wilson College of Textiles together with College of Engineering faculty are working on technology that will help diagnose amputee discomfort in order to make their artificial limbs more comfortable. The research team in the Department of Textile Engineering, Chemistry and Science (TECS), led by Dr. Tushar Ghosh, has been collaborating with teams from the Department of Electrical and Computer Engineering and the Department of Biomedical Engineering, led by Dr. Alper Bozkurt and Dr. Helen Huang, respectively, on developing a uniquely-shaped conductive polymer fiber that, when woven into a fabric structure, forms a multimodal and multifunctional sensor array that can be used with a circuit to sense different stimuli. This innovation offers an unobtrusive way to continuously monitor the many factors that can affect the interaction between an amputee and their artificial limb.
In addition to the myriad challenges amputees already face, they can often experience a nebulous discomfort or a pain in relation to their prosthesis that can be difficult to pinpoint or describe.
“The problem as I understand it from the prosthetists is that they listen to what the amputee has to say, but it is sometimes difficult for them to really understand what’s going on in the socket [the part of the prosthesis that interfaces with or encases an amputee’s residual limb],” said Jordan Tabor, fiber and polymer science doctoral student and TECS teaching and research assistant. “That environment can be really hot and sweaty. There can be strange pressure distributions that lead to things like ulcers…We’re just looking for a better way to understand the environment.”
Ghosh explains that the amputee still has all the sensations of human skin in the residual limb, and when they don an artificial limb, the combination of thick, impermeable sock-like liner and hard prosthesis can be uncomfortable or painful in a number of ways. The research he is overseeing will help change this scenario by collecting continuous data on temperature, humidity, pressure and other factors; the resulting data can help adjust the prosthetic to better distribute pressure and moderate temperature and humidity for an individual amputee.
“Any specific measurement that you can provide to the clinician or prosthetist would help with the discomfort, so that next time the patient comes to visit the doctor, they can do something about it,” said Ghosh. “There are numbers to go by other than just the person saying, ‘I feel kind of itchy here or I have a pain there.’”
How It Works
“The individual, micron-scale, melt-extruded fibers possess three components,” said Tabor. “The first, a conductive polymer material, forms the center of the fiber cross-section that provides the ability to sense. The second, an insulating material, encapsulates the sides of the conductive part and prevents conductive material from touching, thus avoiding electrical issues. Finally, the third sacrificial polymer encapsulates the other polymer components such that the fiber can be made through commercial melt extrusion processing and weaving.”
Once woven, the sacrificial polymer is washed away and the resulting fabric then functions within a circuit as a breathable, flexible touchpad that can sense and transmit a spectrum of data.
“They are made of robust materials that we use every day, like nylon,” said Ghosh. “The conductive part has some carbon in it, which is not harmful to skin and can be cleaned. They are not delicate… [and] the electrical properties are not going to deteriorate easily.”
But how do the conductive fibers actually sense?
“The unique shape of these fibers and the use of a conductive polymer-based material allow the fibers to act as multimodal and multifunctional sensors in a woven structure,” said Tabor. “When woven into a fabric structure, the fibers, as well as the fiber cross-over points, can be used as sensors. The sensor array may be electrically connected to an appropriate electrical circuit to allow sensing of various stimuli.”
So the fibers themselves work as resistive sensors, whose electrical properties change as tension is applied. When woven together, they form capacitive sensors at the fiber junctions; these more complex sensors can sense a variety of stimuli including heat, pressure and moisture levels. Capacitive sensors are at the center of smartphone and tablet computer touchscreen technology.
Researchers developed this novel sensing technology in synergy with teams led by Bozkurt and Huang from the College of Engineering, who also demonstrated a wireless flexible circuit integrated with the product. The next stage of the collaborative experimentation is in vivo clinical studies on amputee subjects.
Other Applications
Potential applications for the technology include doormats that can differentiate among people, a shoe insert that can perform gait analysis and automotive seats that can measure posture.
The research was initially funded by the NC State Chancellor’s Innovation Fund and the Electrical, Communications and Cyber Systems (ECCS) of the National Science Foundation and is currently funded through the Smart and Connected Health program of the National Science Foundation.
Student researchers on the research team include Tabor, as well as Talha Agcayazi, doctoral student in electrical and computer engineering; Aaron Fleming, doctoral student in biomedical engineering; Michael McKnight, Ph.D. in electrical and computer engineering; Ashish Kapoor, TECS doctoral student; Kony Chatterjee, TECS doctoral student; Carrie Gray, TECS undergraduate student, Corey White and Max Gordon, both electrical and computer engineering undergraduate students.
- Categories: