Making an Impact: ZTE Fuels Innovation and Boosts NC Economy
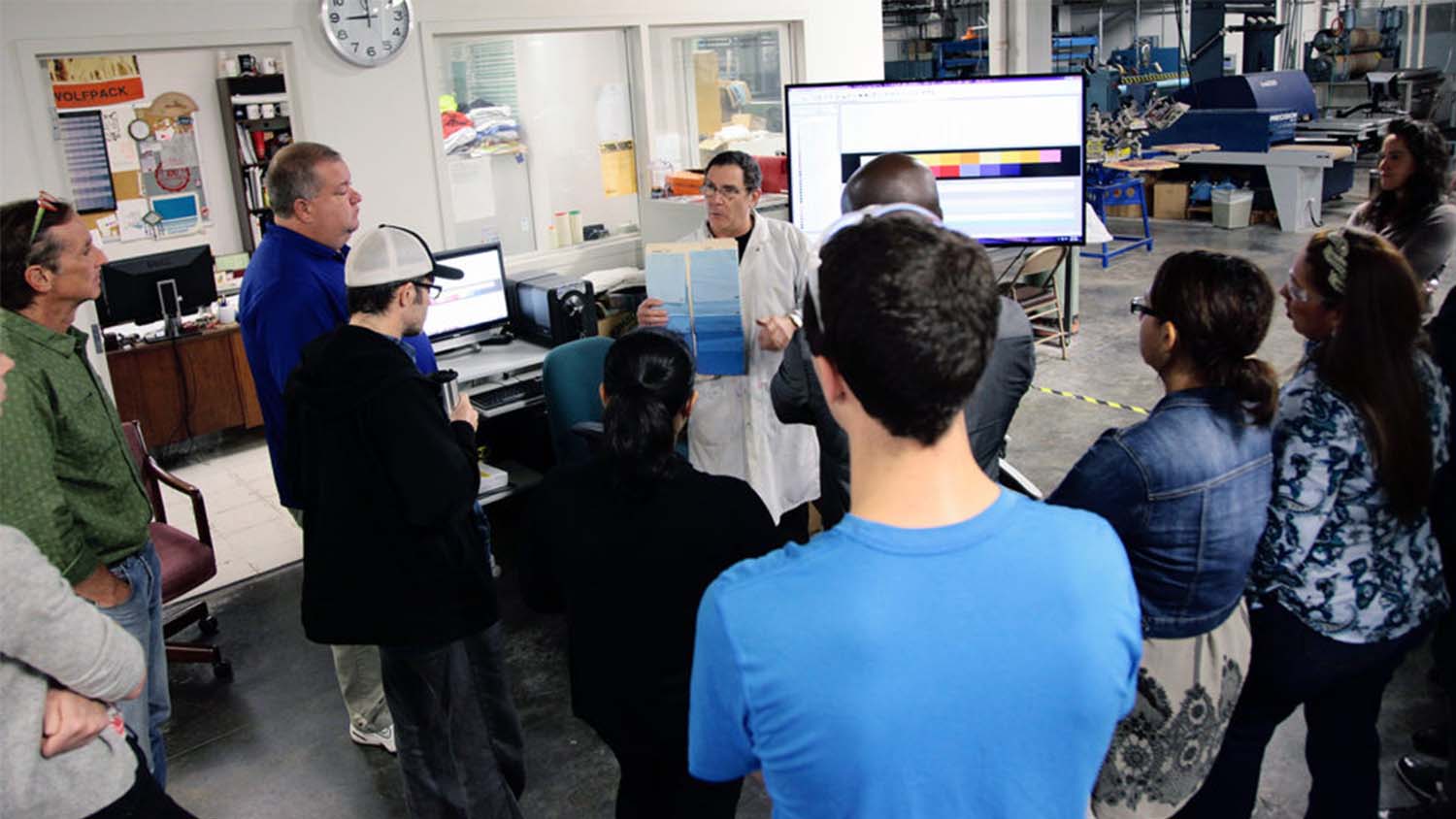
Written by Cameron Walker
Whether a local startup needs help testing a product, a national company wants assistance developing a new fiber or a global business is looking for workforce training, the Wilson College of Textiles is here to help.
The Wilson College of Textiles’ extension department has a long history of partnering with industry; it was formed in 1968 and in its first year delivered short courses in both Charlotte and New York City. In 2006, it was named Zeis Textiles Extension Education for Economic Development to acknowledge a philanthropic commitment from Wilson College of Textiles alumnus Steve Zeis ‘62 and his wife Frosene; since that time, the extension has taught more than 650 courses to nearly 15,000 students with an economic impact in excess of $350 million. More commonly known as Zeis Textiles Extension (ZTE), it was built to foster innovation and offer state-of-the-art education to the textile industry.
“Zeis Textiles Extension exists to serve the constituents of the NC State Wilson College of Textiles including students, staff, faculty, NC State University and industry across the fiber, textile and apparel complex and beyond,” said Dr. Jon Rust, ZTE interim director. “We serve academic institutions around the world; companies in a broad range of industries including healthcare, insurance, banking, retail, apparel, textile and chemical companies; entrepreneurs across the United States and international companies that are considering creating or expanding operations in North Carolina.”
Every Wilson College of Textiles undergraduate student spends time in each of the labs in the course of their education, and many graduate students and faculty use ZTE testing and fabrication labs as part of their research projects. ZTE has also built strong partnerships with industry to provide textile and Lean Six Sigma professional education, textile product prototyping and testing services.
“Our services provide industry with better trained work forces, product R&D and techniques to methodically analyze and improve business process, all of which ultimately strengthen the financial well-being of North Carolina businesses and ultimately that of our state,” said ZTE finance manager Debbie Mostek.
Professional Education
Textile Courses
“Many companies take advantage of our public courses yearly in order to provide some textile knowledge to recent hires or to get specialized training for people whose job responsibilities are changing,” said Rust. “Last year we delivered more than 50 courses…this year, we are adding two new courses including a Smart Textiles workshop.”
The most popular course is Textile Fundamentals, which provides an overview of textile industry terminology and basics including polymers, fibers, knit and woven fabrics, and the processes of dyeing and finishing. Other courses build on this foundation, including Knit and Woven Fabric Design and Development, Technical Textiles, Clothing Comfort and Protection Science, Fiber and Fabric Identification Techniques and more. The courses usually run three to five days long and are open to the public.
“We see a lot of companies in our classes that you would think of, like Patagonia, Nike, UnderArmour, Glen Raven and HanesBrands,” said ZTE office administrator Jan Gaines, who does all logistics for the short courses, including accounting, travel, parking permits, food (which often includes homemade desserts) and the kind of old-fashioned customer service that keeps course attendees coming back. “We have a lot of big corporations, we have a lot of small ones, we have a lot of startups. They come from all over the world — Canada, Japan, China. I remember one particular student was from Australia and he made the trip three times to complete his textile certificate.”
The textile certificate program is a series of five courses — three core and two elective — to be completed within a period of three years. The program is popular with people new to the textiles industry and with those looking to advance their careers.
Lean Six Sigma
Lean Six Sigma is a business philosophy that combines lean manufacturing tools and Six Sigma methodologies to reduce an organization’s costs and increase productivity.
“The best way to think about Lean Six Sigma is improving a process,” said Jeff Blessinger, Master Black Belt and ZTE’s Lean Six Sigma program manager. “Lean deals with removal of waste within a process — not garbage, but wasted activities, inefficiencies. Lean can be thought of as applying common sense to make a process run smoother…Then, Six Sigma deals with analyzing the process to take variation out, because variation leads to errors and quality problems.”
Lean Six Sigma courses, arranged in “belts” like martial arts, teach employees to streamline and perfect processes like manufacturing, customer service or shipping in order to retain customers and improve a company’s bottom line. ZTE offers 11 public Lean Six Sigma courses per year as well as customized in-house training to customers including Michelin Tires, Blue Cross, Novo Nordisk and Campbell’s Soup. The courses are taught in two one-week sections held about a month apart to allow students to apply the concepts they learned in the first section. As part of each course, students must complete a project for their employer; these projects have saved their companies anywhere from thousands to several million dollars. The program certified between 50 and 60 Green and Black Belts last year with an average return on investment of $35 to $1, saving each company about $105,000 per project. One recent Green Belt graduate saved employer BB&T $3 million on a single project.
“Our customers self-reported more than $19 million in economic impact to their companies last year as a result of the projects carried out as part of their certification process through the ZTE Lean Six Sigma program,” said Rust.
But Lean Six Sigma offers other rewards, too. Once problems have been identified and addressed, job satisfaction levels and employee retention numbers improve.
“If a problem has been addressed, people are happier; when they’re happier, they stay longer, they get more productive and they get more involved,” said Blessinger, who runs the program with assistance from program coordinator Latoya Giles. “How do you put a dollar to keeping an employee?”
In 2002, Dr. Blanton Godfrey, then dean of the Wilson College of Textiles, worked with Dr. Tim Clapp and Cliff Seastrunk to develop ZTE’s Lean Six Sigma program, one of the first such programs to be offered in a university setting.
“Lean Six Sigma, in basic terms, is about problem solving and problem prevention that leads to improving and optimizing processes,” said Seastrunk, Lean Six Sigma instructor, Master Black Belt and double NC State alumnus. “It just happens that everything we do is a process — so we can apply the philosophy and tools of Lean Six Sigma to everything we do in our personal and professional lives.”
Seastrunk’s sons, technical sales representative, Jason; Duke Hospital vice president of emergency services, Chad; and patent lawyer, David, have all earned Lean Six Sigma belts.
“I have three sons in three different professions and they will all tell you that their Lean Six Sigma training was extremely beneficial in their careers and getting them where they currently are in their career paths — after all, they all deal with processes in each of their professions,” said Seastrunk.
Due to demand, ZTE is expanding its course offerings and now provides a Lean Six Sigma Green Belt course via distance education.
“This is a big deal,” said Rust. “This allows us to serve a broader audience and deliver course content around the globe. It also allows us to offer Green Belt training and certification at a highly reduced cost to all faculty, staff and students at NC State.”
Custom and Online Training
“The online courses allow industry associates to obtain textile training without leaving the office or plant to travel to Raleigh,” said Mostek. “To date, numerous companies have purchased access to our online courses and in some cases have purchased access for up to 50 associates at a time.”
In addition, Advanced Functional Fabrics of America (AFFOA), a nonprofit institute focused on fiber and fabric innovation, subscribes to Textile Fundamentals eLearning and provides 700 licenses for its member companies’ annual use.
“We offer a Textile Fundamentals eLearning version which is self-paced, includes more than 16 hours of videos, animations, simulations and presentations all narrated by our former dean Robert Barnhardt and with Spanish and Mandarin subtitles,” said Rust. The comprehensive course is divided into 14 chapters, each with a self-assessment; once students receive a score of 80 percent or better on a self-assessment, they receive a certificate of completion of the chapter. Universities in Canada, Japan, Europe and the United States use it as an introduction to textile science and award students credit for their successful completion of the course.
Testing and Fabrication Services
“Our textile fabrication and testing services revenue continue to grow as we continue to modernize our labs, as we are able,” said Rust. “Through donations, partnerships with machinery manufacturers, assistance from the college and university, and as a result of the hard work of our ZTE people in generating receipts, we have made large improvements in replacing outdated equipment for newer and sometimes completely new equipment. If everything goes well in the coming year, we may have our biggest year since 1991 in terms of ZTE textile fabrication laboratory modernization.”
ZTE manages five labs: the Dyeing and Finishing Pilot Plant, the Knitting Laboratory, the Dame S. Hamby Physical Testing Laboratory, the Rieter Short Staple Yarn Laboratory and the Springs Weaving Laboratory, each furnished with cutting-edge equipment and staffed with experienced professionals.
“Zeis Textiles Extension is a place where education and research combine to create a fully functional small scale production facility,” said weaving lab manager William Barefoot. “We are able to help people make their ideas into reality. Being able to help people make their idea into something tangible is exciting, and knowing you might have helped create a new and innovative textile that could change someone’s life is thrilling.”
Last year, the labs provided more than 8,000 hours of service to both student researchers and industry partners, from large entities like manufacturer HanesBrands and specialty chemical company Eastman to small startups.
“We’ve got a lot of potential to help customers do development work and proof of concept for research on medical, industrial, apparel and some that are not your conventional textile topics,” said knitting lab manager Brian Davis.
ZTE personnel provide most of their own salaries through receipts for their services, which can range from standard test methods for physical properties of fibers and fabrics to the development of products that are not thought of as traditional textiles.
“Some of the more interesting products we’ve tested through the years include mosquito bed nets for use in malaria-prone areas, medical products like artificial ACLs, anti-gravity pilot suits, beekeeper suits that are puncture resistant to bee stingers, agricultural barrier fabrics, spider silk fabrics, municipal waste filtration fabric…and the list goes on and on,” said Dr. Jan Ballard, who manages the physical testing laboratory. “My job is never boring because almost every day brings a phone call or an email from someone who needs textile advice, and the questions can sometimes be quite challenging. I like to think that I’ve helped a few folks along the way.”
Partnerships
“ZTE helps a variety of companies ranging from those who are small and yet-to-be-known to those who are prominent around the world,” said Mostek. “It’s exciting to work with the big players but it’s heartwarming to help the companies who are working so hard to start up or who are ready to expand or who want to turn an idea into a tangible product.”
ZTE has recently sponsored several international conferences, including last year’s Textile Summit with participants from around the globe. ZTE regularly works with the Economic Development Partnership of North Carolina (EDPNC) to meet with companies from around the world and educate them about the advantages of locating their operations in North Carolina.
“ZTE personnel are very proud of the impact we have on economic development in the state of North Carolina and beyond,” said Rust.
Last year, ZTE was instrumental in bringing at least three companies to North Carolina, which resulted in more than 600 jobs and over $40 million in capital investments in the state.
“Dr. Jon Rust and Melissa Sharp (ZTE business development coordinator) have consistently furnished absolutely superb technical assistance on dozens of new and expanding industry projects in which our NC State University Economic Development Partnership (EDP) has been engaged,” said Tom White, director of the NC State EDP. “From recruiting new industrial investment and job creation such as Everest Textiles in Rutherford County (610 jobs, $15 million capital investment) to MAS ACME USA in Randolph and Chatham counties (133 jobs, $22 million capital investment), helping retain and expand Brooks Brothers‘ custom shirt manufacturing operation in Sampson County and its companion logistics-distribution center in Clinton, ZTE faculty and staff are truly extraordinary institutional assets to economic and workforce development practitioners throughout the entire state of North Carolina.”
Beyond its ties to industry both local and global, ZTE partners with area community colleges and with national government.
Community Colleges
ZTE partners with community colleges in two areas: LSS training and certification and textile fabrication and testing services. ZTE assists with training the LSS instructors, provides course materials and helps provide certification services for Alamance Community College in Graham, North Carolina and Edgecombe Community College in Tarboro, North Carolina.
“Most of the Lean Six Sigma participants in our public classes come from large companies who pay for it,” said Rust. “Working with the community colleges on Lean Six Sigma allows us to contribute to economic development by serving a segment of the population that wouldn’t otherwise be able to afford it: individuals, entrepreneurs and people working for small companies.”
ZTE has partnered with Dallas, North Carolina’s Gaston College, which houses the Textile Technology Center (TTC), and Hickory, North Carolina’s Catawba Valley Community College, which houses the Manufacturing Solutions Center (MSC), for many years.
“The TTC and the MSC do some of the same things ZTE does in terms of textile fabrication and testing, but mostly, the three complement one another and direct customers to each other depending on the customer’s needs and the capabilities each of us offer,” said Rust.
Government
If you want to see the future, look to the military. The Global Positioning System (GPS), the EpiPen, duct tape, Jeeps, freeze-dried foods, remote control — many of the most significant inventions of the past century were first developed for the United States Armed Forces.
The U.S. Army Natick Soldier Research, Development and Engineering Center (NSRDEC) is in the vanguard of this discovery; its mission is “to provide the Army with innovative science and technology solutions to optimize the performance of our soldiers.” Their research explores subjects in the early stages from concept through component testing and is concerned with equipping the individual soldier with items such as uniforms, tents, parachutes and more. Recent studies have focused on fibers for controlling thermal management.
“One of our core competency areas is textiles and textile technologies, so there’s a huge push to increase the competency of the workforce in textiles,” said William Causey, a textile technologist for the U.S. Army and a part of the Soldier Clothing and Configuration Management Team, who works in research and development for NSRDEC.
A double alumnus of NC State’s Wilson College of Textiles, Causey graduated with a B.S. in Textile Engineering in 2012 and his M.S. in the same in 2014. He was introduced to NSRDEC through a Wilson College of Textiles career fair and took an entry-level position there after graduation. He has helped to shape the center’s partnership with ZTE, including arranging for the Textile Technology Certificate Program to be taught on location at the center, 20 miles west of Boston.
“We are going to be able to get 125 members of the Department of Defense acquisition (staff) through this program, so it’s been really good for beefing up our textile competency,” said Causey. “The training schedule that we are approaching this training with is to have the 125 acquisition workforce members go through the first two cycles then have a cohort go through the program every year or so, to keep a consistent flow following these first five cohorts.”
Three cohorts of 25 members each are nearing completion of the certificate program, and 50 more students are starting the program this spring. Students are all acquisition personnel from the Army, Navy, Coast Guard and other branches of the military.
Causey said the objective of the training is to “strengthen NSRDEC’s posture in the areas of soldier equipment, aerial delivery and expeditionary maneuver support across funding life cycles by reducing programmatic risk and increasing engineering rigor.” To that end, the training is supported by the Army Director for Acquisition Career Management Office’s Section 852 funding.
“The NSRDEC personnel rave about the textile training and they have recently added 15 more weeks of training,” said Rust. “Another great outcome has been the realization from NSRDEC leadership that they need to hire more textile graduates from NC State to go into civilian employment there.”
Causey met with interested students at an information session during the Wilson College of Textiles Career Fair last semester, where he spoke with students who might one day work for the center.
“It’s also been a good opportunity for networking with some of the staff at NC State,” said Causey. “It’s really good being able to have our researchers connect with those professors to build relationships and better understand their research areas…we definitely want to keep the relationship going and then further build our relationship with NC State as a whole.”
ZTE shares the NC State philosophy of “Think and Do.”
“Whether it’s educational or fabrication and testing services, when someone asks if we can help them with a particular need, we do everything we can to assist them,” said Rust. “We don’t look at new problems and say no just because we’ve never done it before. We look for new ways of doing things to solve new problems.”
If ZTE’s capabilities are limitless, it is thanks to its staff — a dedicated, capable, inquisitive group of professionals who are passionate about furthering textile science.
“The people of ZTE are incredible,” said Rust. “Each contributing in their own way, each excelling at the services they provide to our students, staff, faculty, partner companies and really all our constituents. They are a group of leaders in the truest sense: they quickly take the lead for those responsibilities that fall in their circle of authority and they are very willing to provide efficient and effective service to one another as needed. It has been a blessing for me to be able to work with them.”
- Categories: